Importance of Proper Fuse Selection
Fuses play an essential role in protecting electrical circuits from overcurrent conditions, ensuring the safety and reliability of electrical systems. Selecting the correct fuse is more than just a technical detail—it is a safety imperative. An improper fuse may either blow too quickly, disrupting the system's operation, or fail to blow when needed, leading to catastrophic damage. Thus, understanding the various parameters of a fuse and matching them to the specific requirements of your application is crucial for safe and reliable operation.
This guide delves into the key aspects of fuse selection, allowing you to confidently choose the best fuse for your specific application.
Decoding Fuse Data Sheets
The first step in selecting a fuse is accurately interpreting the specifications provided in datasheets. Here is a breakdown of a few critical parameters:
- Rated Current (A): The rated current, sometimes called the nominal current, of a fuse is the maximum current that may be carried without tripping under the specified conditions (i.e., 25°C ambient temperature). This value must be greater than the maximum steady-state current of the application plus some margin. A typical starting point is a current rating of 125-150% of the nominal steady-state current; however, the final decision will depend on the specific behavior and operating conditions of the application. Selecting a fuse with the correct current rating ensures that it will operate reliably under normal conditions while providing protection during overcurrent situations. It is important to consider both the steady-state current and any potential surge currents that might occur, such as inrush during start-up.
- Voltage (VDC/VAC): The fuse’s AC or DC rating is the maximum voltage that can be safely interrupted by the fuse. This value must be equal to or higher than the AC or DC system’s rating. Exceeding this value may lead to arcing, which can result in circuit damage, fire, and other catastrophic failures.
- Interrupting Rating (A @ Rated Voltage): Represents the maximum fault current the fuse can safely interrupt and is typically specified at the fuse’s rated voltage. This parameter is crucial for ensuring the fuse can handle worst-case scenarios, such as short circuits. Currents beyond this value can potentially lead the fuse to rupture, arc, or even explode, among other issues.
- Mounting Type: The choice of mounting type affects more than one might initially suspect, including interrupt ratings, mechanical robustness, ease of replacement, and the physical layout of the circuit. Surface mount packages allow for compact designs; however, they can be thermally sensitive to PCB layout, which may affect the trip current. For field-serviceable equipment, a cartridge fuse is much easier to replace than one that is soldered down. The package also impacts mechanical security. For applications that experience a high degree of shock and vibration, such as EV/HEV applications, a stud-mount fuse is a reliable solution.
- Response Time: This specifies how quickly the fuse reacts to overcurrent and is generally categorized as Time-Delay/Slow Blow or Fast Acting based on response time. Standards such as UL 248 or IEC 60127 define more specific criteria for categorizing fuses based on speed. Slow fuses are ideal for equipment like motors and transformers that experience inrush currents during startup. These fuses can endure temporary, non-damaging spikes while still providing reliable overcurrent protection. Fast Blow fuses provide rapid protection for sensitive electronics, quickly reacting to unexpected overcurrent situations. These fuses are essential for sensitive and safety-related components that could be damaged by even brief overcurrent conditions.
- Plating: High-quality plating materials such as gold, nickel, palladium, silver, or tin are used to improve reliability and performance, with each material offering distinct advantages depending on the application.
Plating Material Key Properties Typical Applications Tin (Sn) - Low cost
- Good solderability
- Moderate corrosion resistance
Standard PCB and general-purpose fuses Nickel (Ni) - Excellent corrosion and wear resistance
- High-temperature stability
- Often used as a base layer
Automotive, aerospace, harsh industrial environments Silver (Ag) - Superior electrical conductivity
- Good corrosion resistance
- Can tarnish over time
High-performance fuses, telecom, power electronics Gold (Au) - Exceptional corrosion resistance
- Stable at low current
- Excellent contact quality
Extremely sensitive circuits, medical, military, aerospace Palladium (Pd) - High corrosion resistance (especially to sulfur)
- Stable, low contact resistance
- Good hardness and wear resistance
- Non-tarnishing
Aerospace, telecom, medical, fuel vapor zones, precision measurement Table 1: Comparison of Fuse Plating Types. - Compliance: Fuses are governed by a range of international and regional standards to ensure consistent performance, safety, and reliability across different applications. Compliance with these standards verifies that a fuse has been independently tested for critical parameters such as interrupting capacity, temperature rise, long-term aging, vibration resistance, and environmental durability. Key standards include UL 248 for low-voltage fuses in North America, IEC 60127 for miniature fuses in global applications, and AEC-Q200 for automotive-grade fuses operating in harsh environments. Selecting a fuse with the appropriate certifications ensures that it meets industry-recognized performance criteria, supports regulatory approvals for end products, and reduces the risk of field failures. For mission-critical applications—such as EV/HEV systems, industrial automation, or medical devices—using fully compliant fuses is essential for maintaining system safety, reliability, and regulatory acceptance.
Understanding Fuse Types
Fuses are critical circuit protection devices that prevent damage from overcurrent faults across a wide range of electronic systems. Distinct types, such as EV/HEV fuses, glass and ceramic fuses, brick fuses, chip fuses, and radial leaded fuses, are designed to meet the unique electrical, thermal, and mechanical demands of specific applications. Choosing the right fuse type is essential for ensuring safety, performance, and long-term system reliability.

- Brick Fuses: Brick fuses, often used in high-current and high-power applications, are specifically designed to deliver robust overcurrent protection in compact, thermally efficient packages. Their solid, rectangular construction allows for excellent thermal management and high mechanical strength, enabling them to withstand demanding operational stresses such as vibration, temperature cycling, and fault energy. Brick fuses feature high interrupting ratings, minimal electrical resistance, and precise time-current characteristics critical for safeguarding power electronics, industrial drives, and energy storage systems. Their advanced performance is essential for maintaining system reliability in environments where space, efficiency, and durability are critical design constraints.
- Chip Fuses: Chip fuses, or surface-mount fuses, are engineered to deliver precise overcurrent protection in compact, space-constrained electronic assemblies. Designed for high-volume automated manufacturing, chip fuses provide fast response to overload conditions while offering excellent thermal and electrical stability on densely populated printed circuit boards (PCBs). Their low-profile and standardized packaging enables easy integration into modern miniaturized devices, including smartphones, tablets, IoT devices, and automotive electronics. Chip fuses are crucial for protecting delicate components against overcurrent faults without introducing significant board stress or complexity, ensuring continued reliability in mission-critical and consumer applications alike.
- EV/HEV Fuses: The rapid growth of electric vehicles (EVs) and charging systems has introduced distinct challenges for fuse technology. The elevated voltage and current levels inherent in EV applications demand fuses with exceptional interrupting ratings and precise reaction capabilities. To address these unique needs, high-voltage EV fuses have been developed specifically for EV applications. These fuses are engineered to provide rapid fault isolation and maintain thermal stability under high-stress conditions. The advanced functionality of EV fuses is critical for ensuring the operational reliability and fault-tolerance of eMobility systems.
- Glass/Ceramic Tube Fuses: Glass and ceramic fuses remain foundational elements in electronic circuit protection, each offering unique advantages tailored to specific environments. Glass fuses provide clear visual indication of fuse status, making diagnostics and maintenance straightforward, but are limited to lower interrupting ratings. In contrast, ceramic fuses offer enhanced arc containment, higher interrupting capacity, and improved thermal resilience, making them suitable for more demanding applications. These fuses are engineered to protect sensitive equipment from overcurrents while maintaining circuit integrity under fault conditions, with ceramic versions especially favored in applications requiring elevated safety margins and high fault-clearing capability.
- Radial Leaded Fuses: These fuses are designed to offer versatile circuit protection for applications requiring through-hole mounting and mechanical durability. These fuses feature two leads extending from a central fuse body, enabling secure anchoring to PCBs and effective resistance to vibration and mechanical shock. Radial lead fuses are available in both fast-acting and time-delay versions, allowing designers to select the optimal response for a wide range of power and signal applications. Their combination of ease of installation, stable thermal performance, and high interrupt ratings makes them ideal for industrial controls, consumer appliances, lighting systems, and automotive subsystems.
Fuse Type | Mounting | Current Range | Main Application |
---|---|---|---|
Brick | Surface mount | 250 mA ~ 100 A | Routers, Blade Servers, Battery Storage Systems |
Chip | Surface mount | 200 mA ~ 50 A | IoT, mobile electronics |
EV/HEV | Stud-mount or through-hole | 5 ~ 800 A | Electric vehicles |
Glass/Ceramic | Through-hole or clip | 40 mA ~ 30 A | Electronics, instrumentation |
Radial Leaded | Through-hole | 80 mA ~ 20 A | Appliances, industrial control, consumer electronics |
How to Read Time-Current Characteristic Curves
Time-current curves, commonly found in datasheets, visualize the amount of time it will take for a fuse to interrupt its circuit under varying current conditions. These graphs help analyze performance and match the fuse to the application’s distinct requirements.
The vertical axis represents the time to open (typically in seconds, on a logarithmic scale), while the horizontal axis shows the applied current (also logarithmic, in units of amperes). This format allows you to quickly assess how a fuse will respond at various current overload levels.
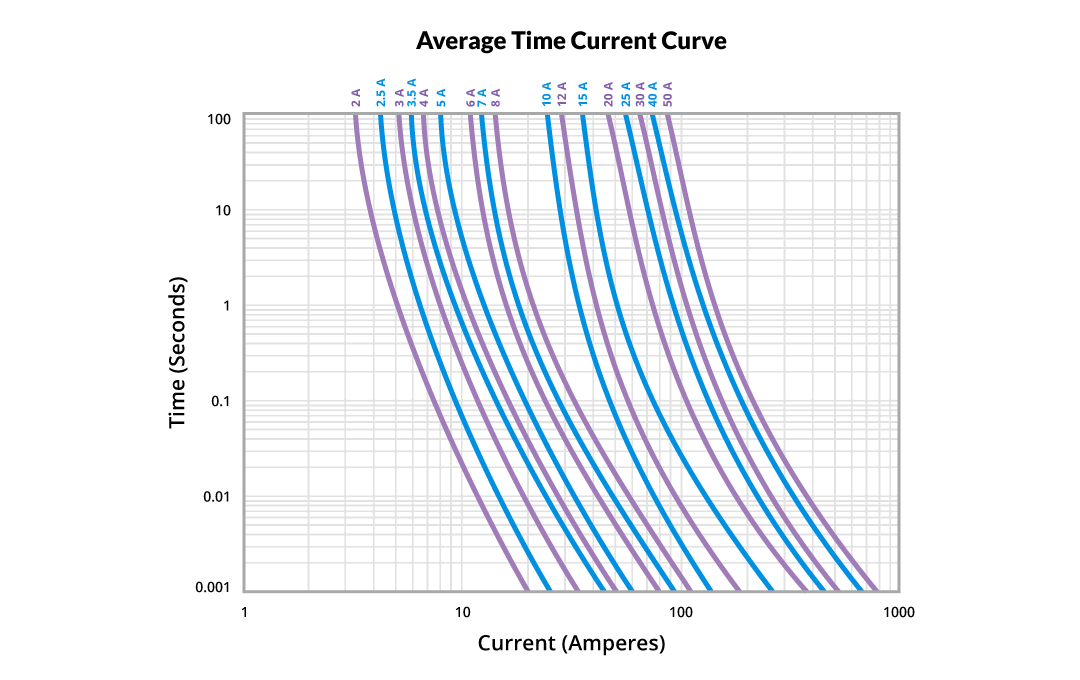
For example, a fast-acting fuse rated at 5 A may open in under 10 milliseconds at 20 A, but might survive indefinitely at 5.5 A. In contrast, a time-delay (slow-blow) fuse of the same rating could tolerate several seconds or even minutes at modest overloads before opening—ideal for circuits with inrush currents, like motors or transformers.
Key Insights When Reading Time-Current Characteristic Curves
- Fuse Speed Classification: Fast-acting fuses have steep, narrow curves indicating quick response times, while slow-blow fuses have flatter, broader curves allowing longer delays at moderate overcurrents.
- Coordination with Load Behavior: Choose a fuse that stays intact during temporary inrush but opens quickly during sustained or dangerous faults. Comparing the fuse curve to expected inrush and steady-state currents ensures proper coordination.
- Application Margining: Always ensure that the normal operating current, including tolerances and transients, stays well below the region where the curve begins to slope steeply downward.
- Multiple Curves for Conditions: Some datasheets offer multiple curves based on ambient temperature, indicating how thermal conditions affect opening times. Higher temperatures typically reduce the time to trip.
By examining the time-current curve, it is possible to predict how the fuse will respond to various levels of overcurrent, ensuring optimal protection for your circuit. However, for operation below 10 milliseconds, the I²t data is typically used.
How to Select Fuses Using Parametric Search
Selecting the right fuse can be a complex task, but Bel’s advanced Parametric Search Tool simplifies the process by allowing engineers to filter options based on critical design criteria. This tool allows engineers to quickly filter available fuse options based on critical parameters such as voltage rating, current rating, interrupting rating, response time, mounting type, compliance standards, and more. By leveraging Bel's extensive parametric search functionality, you can efficiently narrow down the best choices for your specific application, saving valuable design time while ensuring optimal protection and reliability.
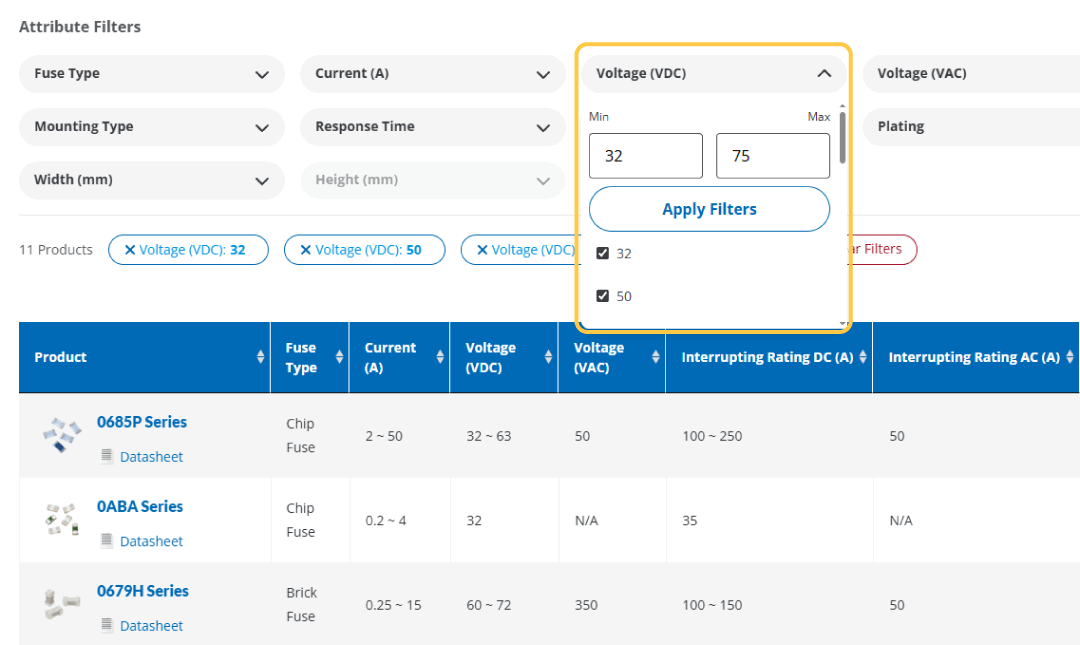
To guide you through the fuse selection process, follow these key steps:
- Define Application Requirements: Identify the overall application type, load behavior, operating conditions, and criticality of the system. Understand whether the system is mission-critical, subject to heavy surges, or designed for sensitive electronics.
- Determine Voltage Rating: Ensure the fuse can handle the maximum operating voltage of your application. The fuse’s voltage rating must be equal to or greater than the system voltage to prevent arcing and ensure safe interruption under fault conditions.
- Determine Current Rating: Calculate the system’s normal steady-state current. Add a safety margin (typically 125–150%) to account for startup inrush or transient surges. If the application has large inrush currents (e.g., motors, capacitors), plan for time-delay behavior.
- Select an Appropriate Interrupting Rating: Identify the maximum available fault current. Choose a fuse whose interrupting rating exceeds this value to ensure safe disconnection under short-circuit conditions.
- Define Response Time Requirements: Decide whether fast-acting or time-delay response is needed:
- Fast-Acting: For sensitive electronics without inrush.
- Time-Delay (Slow-Blow): For loads like motors, transformers, or capacitive input supplies.
- Assess Environmental Conditions: Analyze external conditions like ambient temperature, humidity, dust, vibration, mechanical shock, and operating altitude. Confirm the fuse is rated for environmental durability under expected stresses. Remember to apply thermal derating, if applicable.
- Determine Mechanical and Mounting Requirements: Select an appropriate package and mounting style based on space limitations, thermal management needs, PCB layout, and mechanical security. Consider whether field-serviceability (easy replacement) is important.
- Confirm Compliance and Certification Requirements: Verify whether the application demands compliance with specific standards, such as AEC-Q200 (for automotive applications), UL 248 (for low-voltage fuses), or IEC 60127 (for miniature fuses). Ensure the selected fuse complies and/or is certified to all relevant regulatory and reliability standards for your target market.
- Select Fuse Type: Determine whether a Brick, Chip, EV/HEV, Glass/Ceramic Tube, or Radial Lead fuse best suits your design. Consider the physical and electrical characteristics of each fuse type in relation to your application.
- Evaluate Results: Use Bel’s Parametric Search Tool to narrow down candidates. Review datasheets against the voltage, current, interrupt rating, response time, mounting, size, and certification. View and download 3D models and PCB footprints to view in your design.
- Validate Final Selection: Perform a final review under worst-case operating conditions (e.g., highest fault current, lowest ambient cooling). Ensure the fuse will reliably protect the system in all expected real-world scenarios.
Ensuring Safety and Efficiency with Proper Fuse Selection
Choosing the right fuse safeguards your devices and systems, offering peace of mind and preventing costly damage. A well-selected fuse acts as a critical component in maintaining the safety and functionality of electrical systems. By following this comprehensive guide, you can make informed decisions that enhance the longevity of your devices.
Ready to find the perfect fuse for your application? Explore Bel’s Parametric Search Tool and easily filter by voltage, current, response time, and more.