In industrial automation, reliable power is essential for seamless operations and minimizing costly downtime. This article explores five critical challenges in selecting industrial power supplies and provides solutions to ensure reliability:
- Managing power fluctuations for stability
- Reducing downtime with robust supplies
- Designing for harsh environments
- Improving energy efficiency and sustainability
- Adapting to IoT and smart technologies
Power in Industrial Automation
The explosion of industrial automation technologies over the past decade has brought many benefits, including increased productivity, improved efficiency, and enhanced decision-making capabilities. However, with the inclusion of internet-enabled sensors and steady rise of AI and predictive systems, the reliance on data has also increased, making data quality and reliability critical factors in industrial operations.
In today's data-driven industrial landscape, where sensors and systems are connected to the internet, and advanced predictive systems are making decisions in real-time, a robust power supply is essential for maintaining high levels of output and performance.
Challenge 1 – Managing Power Fluctuations in Industrial Systems
Industrial systems are highly prone to power fluctuations, which pose significant challenges for industrial power supplies. These systems, with complex sensor and control networks spanning large areas, often include power-hungry devices like motors that generate significant voltage transients on the AC mains. These fluctuations can result in under-voltage or over-voltage conditions, leading to brown-outs, equipment instability, and even failures.
Unmitigated voltage transients can pass through the power supply, disrupting the output and damaging connected devices. Furthermore, connected loads using pulse-width modulation (PWM), such as laser heads and CNC spindles, can cause back-propagating transients, destabilizing other devices and impacting system performance.
To combat these issues, advanced industrial power supplies integrate features like:
- Enhanced Isolation Strength
- Robust EMI Filtering
- Transient Suppression
- Extended Hold-up Times for Momentary Power Loss Mitigation
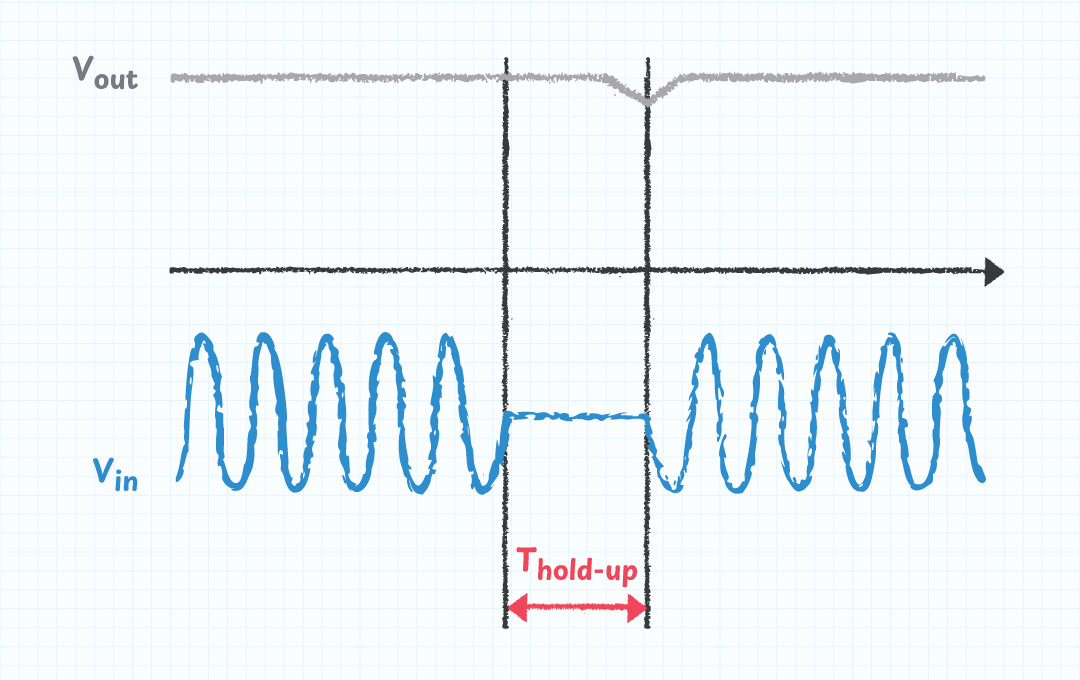
Challenge 2 – Mitigating Downtime Due to Power Failures
In industrial automation, downtime is a critical issue that can lead to significant economic losses, production delays, and compromised efficiency. With industrial processes designed to operate 24/7, even a brief disruption can ripple through supply chains, halting operations and escalating costs. As a result, every component in the system—particularly the power supply—must be carefully engineered to ensure reliable, uninterrupted performance.
The high-power demands of motors, sensors, and controllers, coupled with the tightly integrated nature of industrial ecosystems, mean there’s little room for backup systems. This makes the reliability of the primary power supply paramount. Robust industrial power supplies are engineered to minimize failure points, using simplified designs and high-quality components to ensure longevity and dependability.
To prevent downtime, power supplies must incorporate protection mechanisms, including over-voltage, over-current, and over-temperature safeguards. These features are essential for shielding downstream devices—often significantly more valuable than the power supply itself—from damage. Protecting these critical assets is vital to maintaining operational continuity and avoiding costly repairs or replacements.
In situations where downtime is absolutely intolerable, reduntant power systems may be necessary. In these cases, power supplies must support seamless transitions and comprehensive power monitoring to ensure uninterrupted operations. Whether through redundancy or extreme reliability, industrial power supplies play a pivotal role in minimizing downtime and maintaining productivity.
Challenge 3 – Resilience in Harsh Operating Environments
Industrial environments often subject electronic systems to harsh conditions that push the limits of power supply performance. From extreme temperatures causing thermal stress to mechanical vibrations from heavy machinery, the challenges are numerous. Industrial applications frequently operate in temperature ranges from as low as -40°C in cold storage or outdoor settings to as high as 85°C or more in environments near heat-generating equipment or in direct sunlight. These extreme conditions necessitate power supplies capable of operating reliably across wide temperature ranges without degradation.
In such environments, de-rating is often required to ensure power supplies can perform safely and reliably. De-rating involves operating a power supply below its maximum specified capacity to account for environmental stresses, such as high temperatures or continuous heavy loads. For instance, a power supply rated for 100% output at 25°C may need to be de-rated by 20–30% when operating at 70°C to prevent overheating and premature component failure. Similarly, de-rating may also be applied to handle mechanical vibrations, prolonged operational cycles, or variations in input voltage.
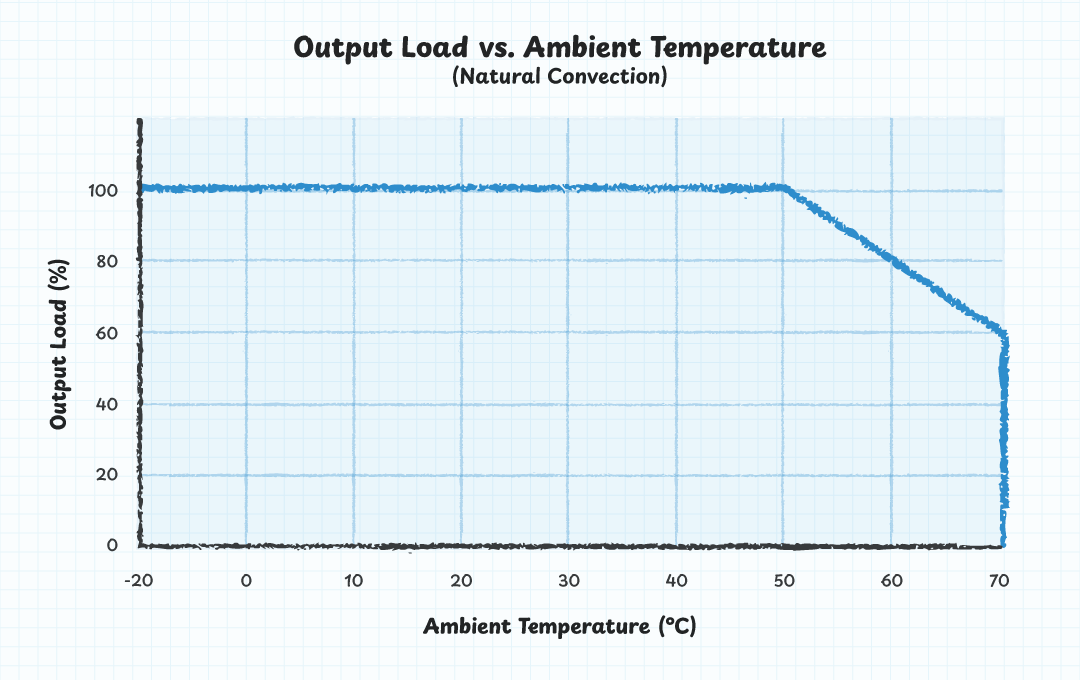
Additionally, humidity fluctuations, corrosive or explosive atmospheres, and other pollutants further compound the risks. To mitigate these risks industrial power supplies must incorporate additional protective features such as conformal coatings, sealed enclosures, and ruggedized construction designed to resist these environmental hazards.
Electromagnetic compatibility (EMC) another significant concern in these environments. Industrial systems demand high reliability and safety, requiring power supplies to both resist electromagnetic interference (EMI) and prevent the emission of disruptive noise that could affect surrounding equipment. Power supplies designed for class B environments can help limit the amount of EMI being emitted into the system compared to class A rated power supplies more commonly found in industrial applications.
Challenge 4 – Energy Efficiency and Sustainability
Rising energy costs are placing significant pressure on industrial operations to enhance efficiency and reduce waste. Achieving this requires not only optimizing motors, drive systems, and production equipment but also addressing inefficiencies in power conversion and conditioning processes, which often result in unnecessary energy losses. These losses, while subtle, can accumulate into substantial operational costs and environmental impact.
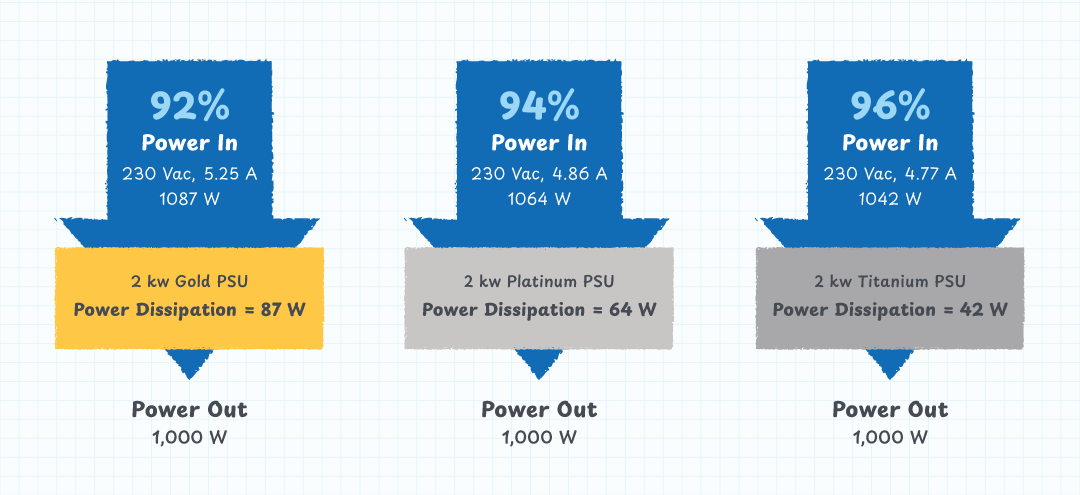
High-efficiency industrial power supplies play a critical role in mitigating these challenges. By maximizing energy conversion efficiency, these power supplies lower operating costs, reduce heat generation, and enable more compact designs. This not only decreases the overall size and weight of equipment but also allows for higher power densities, making systems more versatile and cost-effective.
Beyond cost savings, efficient power supplies support sustainability goals by minimizing energy consumption and environmental impact. Businesses aiming to reduce their carbon footprint and comply with increasingly stringent environmental regulations will benefit from adopting greener technologies, including advanced power supply designs.
Challenge 5 – Integration with Smart Systems
The rise of the Industrial Internet of Things (IIoT) has transformed the industrial landscape, creating a demand for smarter, more connected systems. While sensors, controllers, and other devices have rapidly adapted to this shift, power supplies have often been slower to evolve. However, as the need for reliability, advanced decision-making, and real-time monitoring grows, integrating connected power supplies into industrial installations is becoming a critical priority.
Connected power supplies offer significant advantages, including the ability to enable real-time monitoring and remote control. By leveraging communication protocols such as SMBus and PMBus, these power supplies can transmit system data and accept remote commands. This capability allows operators to monitor critical parameters, adjust settings, and respond to potential issues without the need for on-site intervention, improving efficiency and reducing response times.
Another key benefit is the enhancement of predictive maintenance. With real-time data collection, connected power supplies can identify anomalies, such as voltage fluctuations or thermal irregularities, before they lead to equipment failures. This proactive approach minimizes downtime, extends equipment life, and improves overall system reliability, which is essential for 24/7 industrial operations.
Powering Industrial Automation with Bel
Industrial automation demands reliable, efficient, and adaptable power supplies to overcome challenges like downtime, harsh environments, and energy inefficiencies. Bel meets these needs with a comprehensive range of innovative power solutions, from low-power board mounts to high-power enclosed designs with advanced communication and control capabilities. With flexible designs and expert support, Bel empowers engineers to customize solutions for seamless integration into any system.
Industrial automation demands reliable, efficient, and adaptable power supplies to overcome challenges like downtime, harsh environments, and energy inefficiencies. Bel meets these needs with a comprehensive range of innovative power solutions, from low-power board mounts to high-power enclosed designs with advanced communication and control capabilities. With flexible designs and expert support, Bel empowers engineers to customize solutions for seamless integration into any system.
Explore how Bel’s power supplies can elevate your industrial automation systems by visiting our Industrial Power Solutions page.